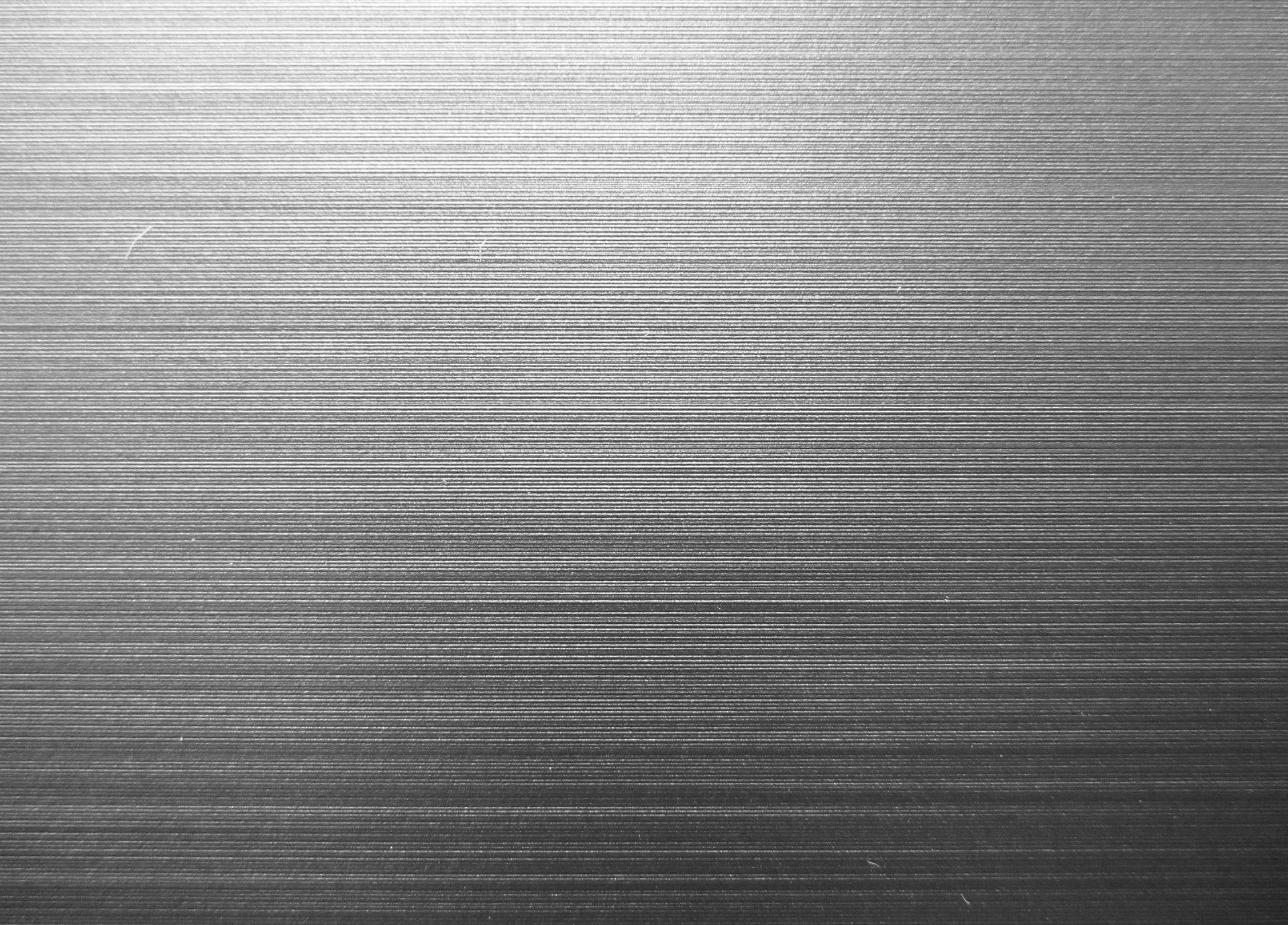
Ask 8 Questions
-
What is air used for (acfm or m3/min)?
-
What pressure is required (bar)?
-
What is the electrical supply (voltage)?
-
How does existing compressor cope?
-
What is the model, size and kW of existing compressor?
-
Future demand required?
-
Do you require a refrigerant air dryer & line filters?
-
Do you require an air receiver?
What size compressor do I require?
Maintenance
Daily Operation - Prior to starting the compressor, it is necessary to check the fluid level in the oil tank. Should the level be low, simply add the necessary amount of oil. If the addition of the fluid becomes too frequent, a simple problem has developed which is causing this excessive loss. See the Troubleshooting Section under Excessive Fluid Consumption for a probable cause and remedy. After a regular start has been made, observe the instrumental panel gauges and be sure they monitor the correct reading for this particular phase of operation. After the compressor has warmed up, it is recommended that a general check on the overall compressor and instrumental panel be made to assure that the compressor is running properly.
-Do not remove caps, earplugs or other components when the compressor is running or pressurized.
-Stop the compressor and relieve all internal pressure before doing any work.
What is Ultrasonic Testing?
Many electrical and mechanical problems produce sound and vibration at ultrasonic frequencies (greater than 20kHz). Unfortunately, these sounds cannot be detected by the human ear. These sounds can be detected by ultrasonic listening instruments. These instruments have been integrated into our Predictive Testing Service.
Ultrasonic testing is used in two ways in our Predictive Testing Service. First, it permits us to identify faults that cannot be detected by either infrared or vibration tests. Second, it permits an independent verification of problems that can be detected by the infrared or vibration tests.
​
Any type of impacting mechanical fault will generate ultrasound. Such faults in clude bearing and gear defects as well as mechanical looseness. Ultrasonic testing generally provides earlier warning of these types of faults than vibration or infrared tests.
Other mechanical faults that are found by ultrasound include: defective steam traps; leaks in pipes or vessels due to faulty welds, holes, gasket failures, etc.;leaky valves in liquid or gas lines and leaks in compressed air systems. Compressed air leak surveys can be a particularly valuable process that can easily reduce compressed air demand and electrical usage.
Ultrasonic survey of high voltage power lines. The sensitivity of the instrument is greatly enhanced for this application by using a parabolic signal concentrator.
Ultrasound is extremely valuable for inspections of high voltage electrical systems (above 2,000V). These systems require properly functioning insulation systems. Failure of high voltage insulation systems can result in catastrophic faults. Deterioration of high voltage insulation produces an electrical leakage known as corona, tracking or partial discharge. This condition causes ionization of the surrounding air. The ionization process produces ultrasound which is readily detected by the ultrasound instrument.
What is Hydrostatic Testing?
A hydrostatic test is a way in which pressure vessels can be tested for strength and leaks. The test involves filling the vessel or pipe system with a liquid, usually water, which may be dyed to aid in visual leak detection, and pressurization of the vessel to the specified test pressure. Pressure tightness can be tested by shutting off the supply valve and observing whether there is a pressure loss. The location of a leak can be visually identified more easily if the water contains a colorant. Strength is usually tested by measuring permanent deformation of the container. Hydrostatic testing is the most common method employed for testing pipes and pressure vessels. Using this test helps maintain safety standards and durability of a vessel over time. Newly manufactured pieces are initially qualified using the hydrostatic test. They are then re-qualified at regular intervals using theproof pressure test which is also called the modified hydrostatic test.Testing of pressure vessels for transport and storage of gases is very important because such containers can explode if they fail under pressure.
​
Hydrostatic tests are conducted under the constraints of either the industry's or the customer's specifications, or may be required by law. The vessel is filled with a nearly incompressible liquid - usually water or oil - pressurised to test pressure, and examined for leaks or permanent changes in shape. Red or fluorescent dyes may be added to the water to make leaks easier to see. The test pressure is always considerably higher than the operating pressure to give a factor of safety. This factor of safety is typically 166.66%, 143% or 150% of the designed working pressure, depending on the regulations that apply. For example, if a cylinder was rated to DOT-2015 PSI (approximately 139 bar), it would be tested at around 3360 PSI (approximately 232 bar). Water is commonly used because it is cheap and easily available, and is usually harmless to the system to be tested. Hydraulic fluids and oils may be specified where contamination with water could cause problems. These fluids are nearly incompressible, therefore requiring relatively little work to develop a high pressure, and is therefore also only able to release a small amount of energy in case of a failure - only a small volume will escape under high pressure if the container fails. If high pressure gas were used, then the gas would expand to V=(nRT)/p with its compressed volume resulting in an explosion, with the attendant risk of damage or injury. This is the risk which the testing is intended to mitigate.
Small pressure vessels are normally tested using a water jacket test. The vessel is visually examined for defects and then placed in a container filled with water, and in which the change in volume of the vessel can be measured, usually by monitoring the water level in a calibrated tube. The vessel is then pressurized for a specified period, usually 30 or more seconds, and if specified, the expansion will be measured by reading off the amount of liquid that has been forced into the measuring tube by the volume increase of the pressurized vessel. The vessel is then depressurized, and the permanent volume increase due to plastic deformation while under pressure is measured by comparing the final volume in the measuring tube with the volume before pressurization. A leak will give a similar result to permanent set, but will be detectable by holding the volume in the pressurized vessel by closing the inlet valve for a period before depressurizing, as the pressure will drop steadily during this period if there is a leak. In most cases a permanent set that exceeds the specified maximum will indicate failure. A leak may also be a failure criterion, but it may be that the leak is due to poor sealing of the test equipment. If the vessel fails, it will normally go through a condemning process marking the cylinder as unsafe.
The information needed to specify the test is stamped onto the cylinder. This includes the design standard, serial number, manufacturer, and manufacture date. After testing, the vessel or its nameplate will usually be stamp marked with the date of the successful test, and the test facility's identification mark.
A simpler test, that is also considered a hydrostatic test but can be performed by anyone who has a garden hose, is to pressurize the vessel by filling it with water and to physically examine the outside for leaks. This type of test is suitable for containers such as boat fuel tanks, which are not pressure vessels but must work under the hydrostatic pressure of the contents. A hydrostatic test head is usually specified as a height above the tank top. The tank is pressurized by filling water to the specified height through a temporary standpipe if necessary. It may be necessary to seal vents and other outlets during the test.
​
For All Sales, Services And Repairs
Contact Us
021 981 8610